View My LinkedIn Profile
View My Google Scholar
View My Research Lab
I'm a Materials Scientist and a Mechanical Engineer at MIT. My background at the intersection of materials science, mechanical/chemical engineering positions me to understand and efficiently tackle real-world challenges in areas such as crystallization science, materials synthesis, carbon capture, energy storage, techno-economic modelling, automotive emissions, and renewable energy technologies.
View My GitHub Profile
Atmospheric Water Capture
Atmospheric Water Capture (AWC) refers to the capture and collection of water from air in the form of vapor or small droplets and has tremendous potential to address global shortage of clean drinking water.
Based on the RH (Relative Humidity) conditions, AWC methods can vary. For RH>90%, AWC can be accomplished using a simple high-density mesh/warping which can extrct several liters of water per day, at RH>60%, dewing can be used and at low RH below 60% in arid climates, hydrophilic sorbents are the most effective in capturing moisture.
- MOF (Metal-Organic Framework) sorbents exhibit steep water uptake capacities with cyclic stability and can be regenerated at low temperatures produced by low-grade heat from sunlight.
- MOFs are crystalline coordination complexes consisting of organic linkers and inorganic polynuclear clusters forming highly ordered 2D and 3D structures.
- Ni2Cl2(BTDD), a novel MOF exhibits a record gravimetric water uptake capacity of 0.82 g/g under simulated desert daytime (45 °C, 5% RH) and nighttime (25 °C, 35% RH) conditions is synthesized using a continuous flow chemistry platform.
Major Outcomes from the Research
- Developed a semi-automated flow synthesis platform with a wide operational window for ultrafast synthesis of MOFs and Zeolites.
- Rapid optimization of synthesis space parameters such as reaction temperature, residence time, amount of solvents with systematic use of DoE (Design of Experiments) to help early stage high-throughput materials discovery.
- Ideal synthesis conditions in flow resulted in reduced methanol and hydrochloric acid volumes in the precursor mixture by 50% and 40% respectively, while achieving threefold increase in productivity compared to batch synthesis.
Relevant Publications for Further Reading and Device Operation
- The reactor module comprised of PTFE tubing held together using an aluminum (Al) core and Al jacket, inserted into an electrically heated furnace allowing for nearly isothermal operation with ultrafast heat transfer, resulting in short residence times needed to achieve the desired product yield.
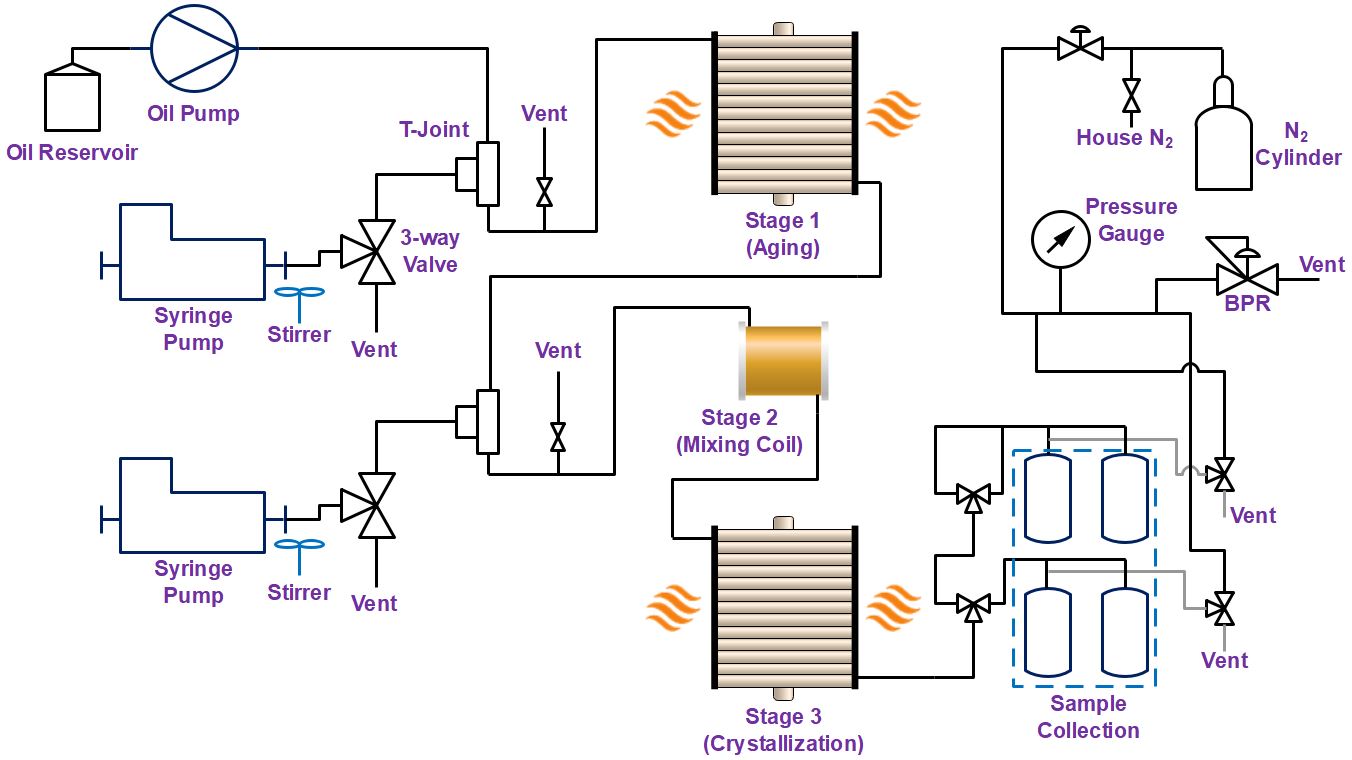
Phenomenological model of crystallization in biphasic liquid-liquid slug flow
- The MOF precursor mixture comprising of NiCl2.6H2O and H2BTDD dissolved in N,N-DMF, CH3OH and HCl, is injected into a continuous stream of silicone oil using a T-junction generating a segmented biphasic slug flow.
- Silicone oil was used as it preferentially wets the hydrophobic surface of the PTFE tubing, thereby producing a continuous phase wherein the MOF precursor can travel as discrete and uniformly spaced droplets within the tube.
- The slug generation process is associated with the dynamic pressure profile existing at the T-junction when two immiscible fluids are simultaneously introduced in the stream. When the stream of first phase is flowing through the junction, the flow of the second phase is obstructed due to immiscibility of the two phases, resulting in pressure build up.
- When the pressure reaches a critical point, the first phase is driven back from the T-junction shearing off the droplet into the stream, thereby generating a slug. This alternated cyclic build-up and release of pressure is responsible for the segmentation of the liquids allowing reproducible slug lengths.
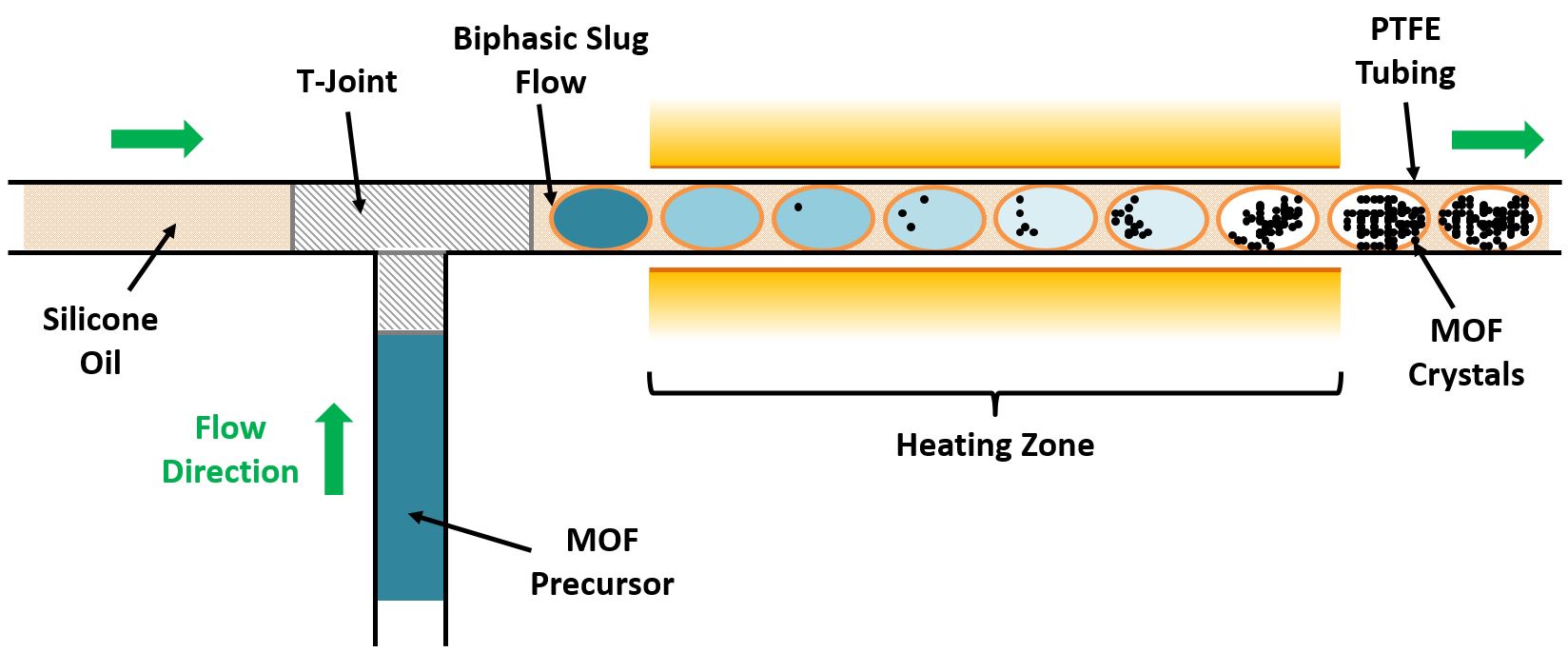
Ni2Cl2(BTDD) MOF featuring 1D pore channels and zig-zag SBUs
- The pores are defined by one-dimensional chains of five coordinate metal atoms with hydrophilic open coordination sites supported by strong metal−azolate linkages.
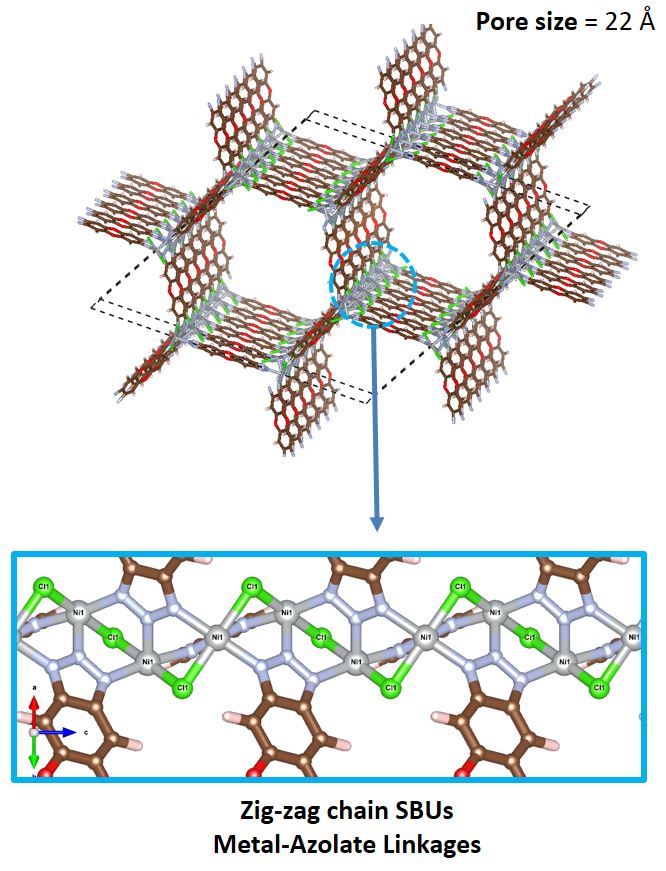
Gravimetric water-uptake isotherms with deliverable capacity and cycling stability
- All materials show type IV isotherms featuring a step in the uptake at approximately 0.28 P/Po (equivalent to RH = 28%), which is attributed to the onset of pore filling.
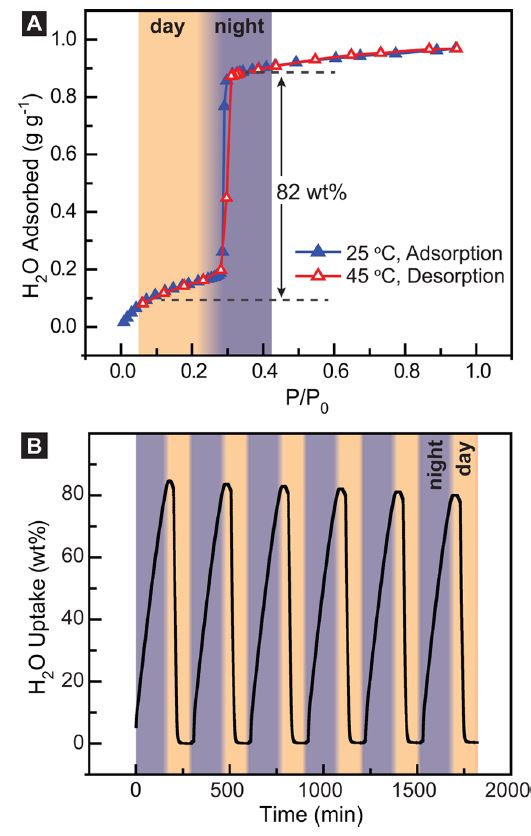
MOF Opportunity landscape with reduced synthetic costs
- Current global market size of MOFs is ~$70 million as of 2019 and is expected to grow at 34% CAGR till 2024 (~$410 million).
- Only a handful of MOFs are commercially available with a quoted market price of >$30/g, while any successful application would require MOF prices to be lower than $0.2/g.
- Based on our techno-economic model, ~80-85% of the synthesis cost originate from the raw materials such as solvents, and organic linkers, while ~15% of the cost originates form energy & equipment cost.
- We firmly believe that the use of flow-reactors for scaled-up production of promising MOF candidates would lead to reduced synthesis costs aiding their quicker adoption in industrial applications.
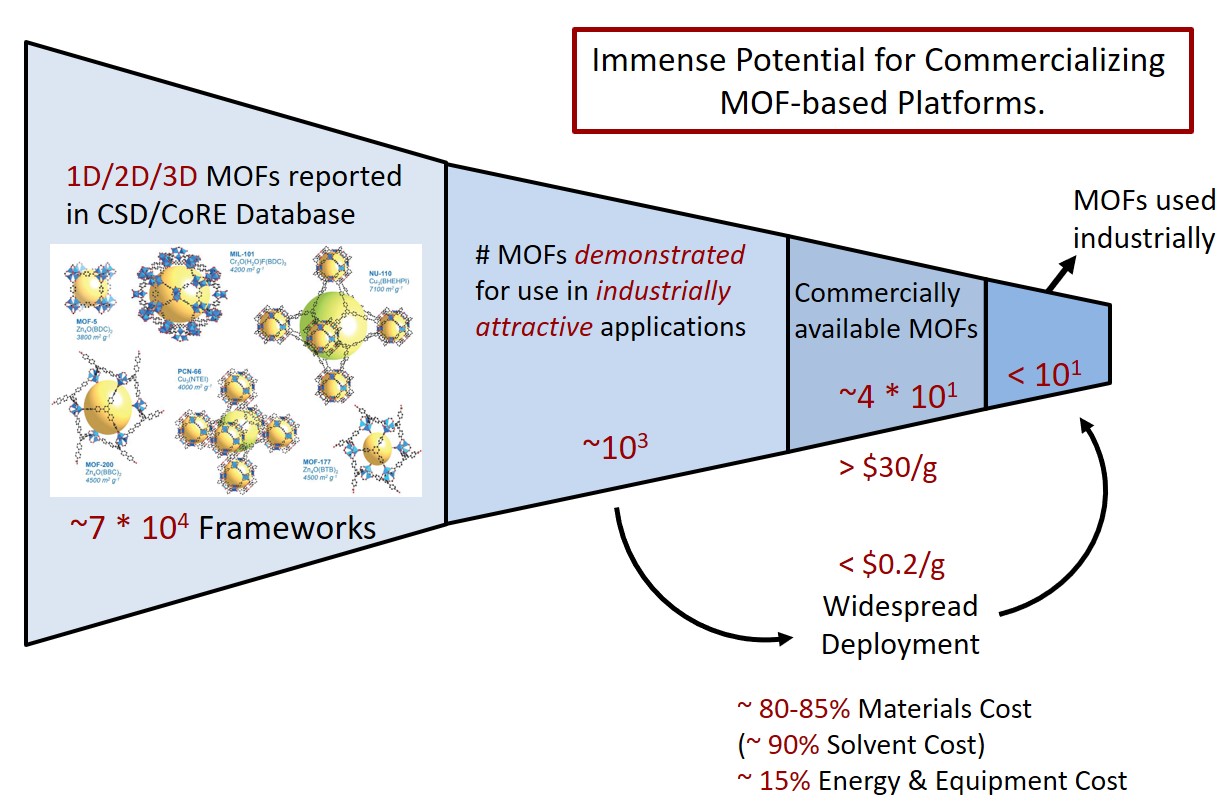