View My LinkedIn Profile
View My Google Scholar
View My Research Lab
I'm a Materials Scientist and a Mechanical Engineer at MIT. My background at the intersection of materials science, mechanical/chemical engineering positions me to understand and efficiently tackle real-world challenges in areas such as crystallization science, materials synthesis, carbon capture, energy storage, techno-economic modelling, automotive emissions, and renewable energy technologies.
View My GitHub Profile
TEA Research Summary
Techno-economic Analysis (TEA) is used to access the batch and flow processes which are used to synthesize porous materials (MOFs and Zeolites). TEA compares the processes in terms of synthesis costs, benefits, risks, and uncertainties.
I present a TEA framework which we developed to quantify the production costs (materials, energy and equipment cost) involved to synthesize MOF-808 in batch and flow reactors.
MOF-808 exhibits outstanding hydrothermal and chemical stability in a wide operating conditions and is a promising material for use in catalysis, adsorption, separation, drug deliver and others.
- A process-based cost estimation methodology was employed to access production costs, which mimics the actual steps of synthesis (from raw materials to finished product) and determines the final cost by summing individual costs incurred in each of the steps.
- A typical lab-scale synthesis starts with dissolving reagents such as metal salt and linker in organic solvents to form the reaction mixture, which is then heated to crystallize MOF particles.All steps for batch and flow syntheses remain the same except the crystallization process owing to differences in the equipment used.
- The cost associated for executing each unit operation (e.g. crystallization, separation etc.) are added to generate the total cost of synthesis in $/g for flow and batch syntheses.
- We model two production scenarios to quantify cost and energy associated with lab-scale flow and batch syntheses. Scenario 1: One time synthesis – represents a typical laboratory operation where MOF is manufactured intermittently in small quantities ca. hundreds of mg scale, which is used for characterization and exploratory work, and Scenario 2: Continuous Production – representing a manufacturing environment where equipment is run continuously to achieve maximum production rates.
Major Outcomes from the TEA
- Switching from an intermittent to a continuous production resembling an industrial-scale operation lowers the total synthesis cost of MOF-808 to $11.3/g in batch and $3/g in flow, representing an expected reduction by ~85% and ~60% respectively.
- Lower cost of materials in flow synthesis results from the use of concentrated precursor mixtures that yield higher amount of crystalline solids on a volumetric basis of reaction mixture compared to batch.
- Flow synthesis sees a dramatic reduction in the use of DMF by ~84% and formic acid by ~67% on a volumetric basis of the reaction mixture compared to batch, resulting in lower costs and a greener process, highlighting the direct benefits of using a concentrated reaction mixture.
- Since electricity is the only form of energy input required for the synthesis, process emissions originate only from the electricity grid and vary linearly as a function of energy consumed in the process.
- Energy intensity of the flow synthesis compared to batch is lower by two orders of magnitude in scenario 1 and an order of magnitude lower in scenario 2, demonstrating significant improvements in energy efficiency achieved in flow.
Simplified block diagram of the synthesis and system boundaries for the batch and flow process
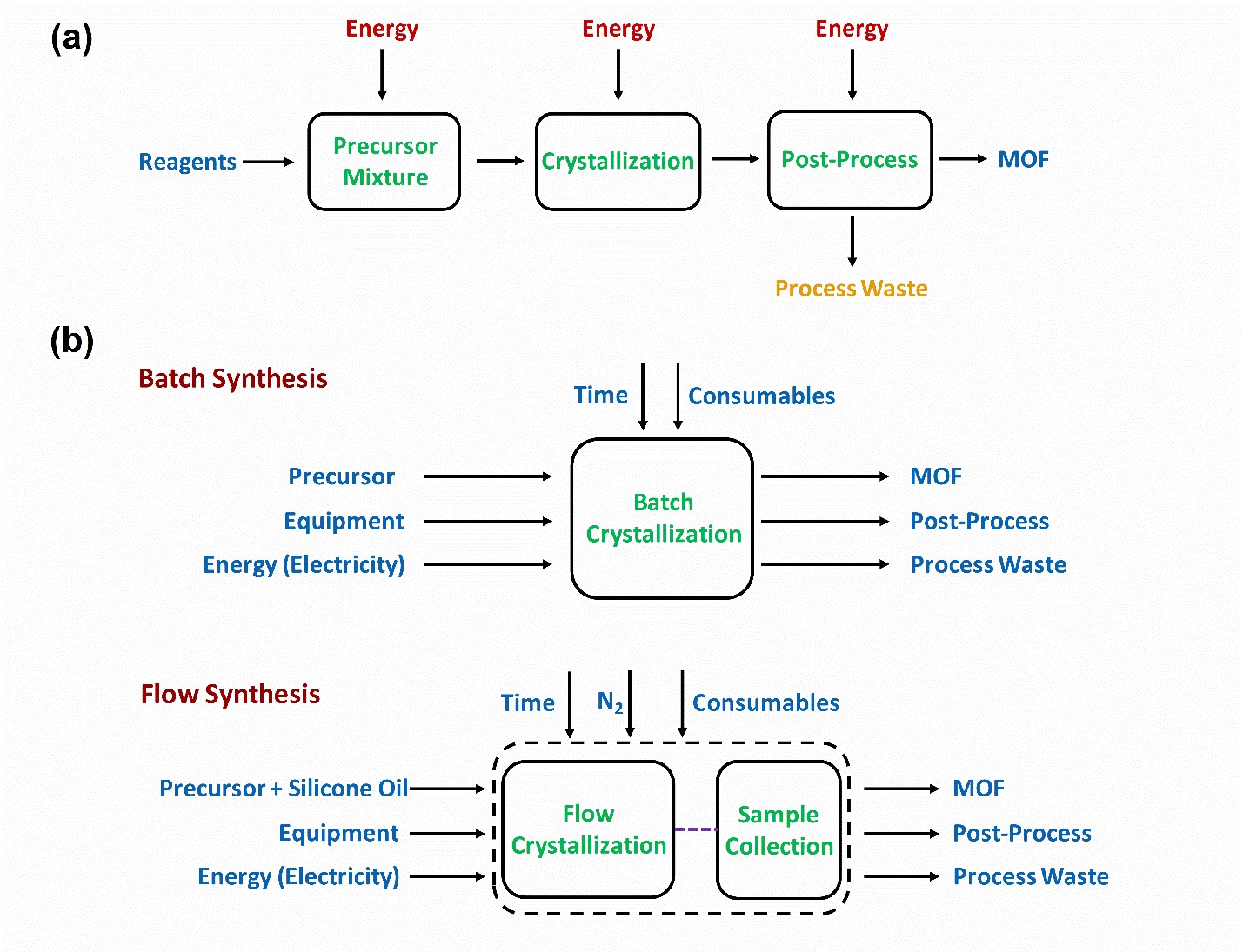
Illustration of Scenarios 1 and 2 in batch and flow process
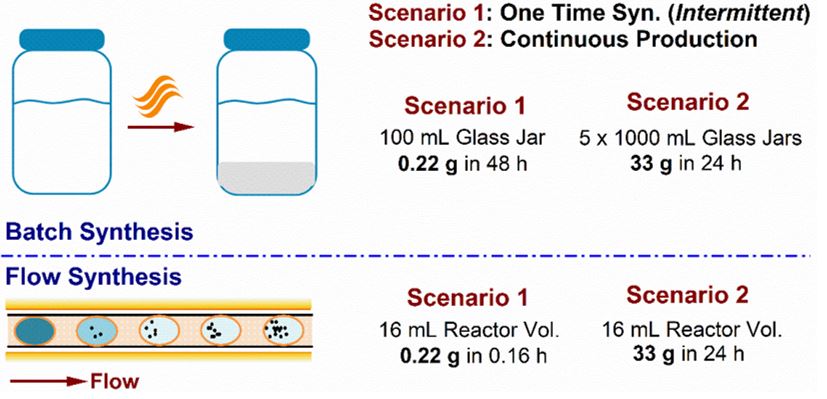
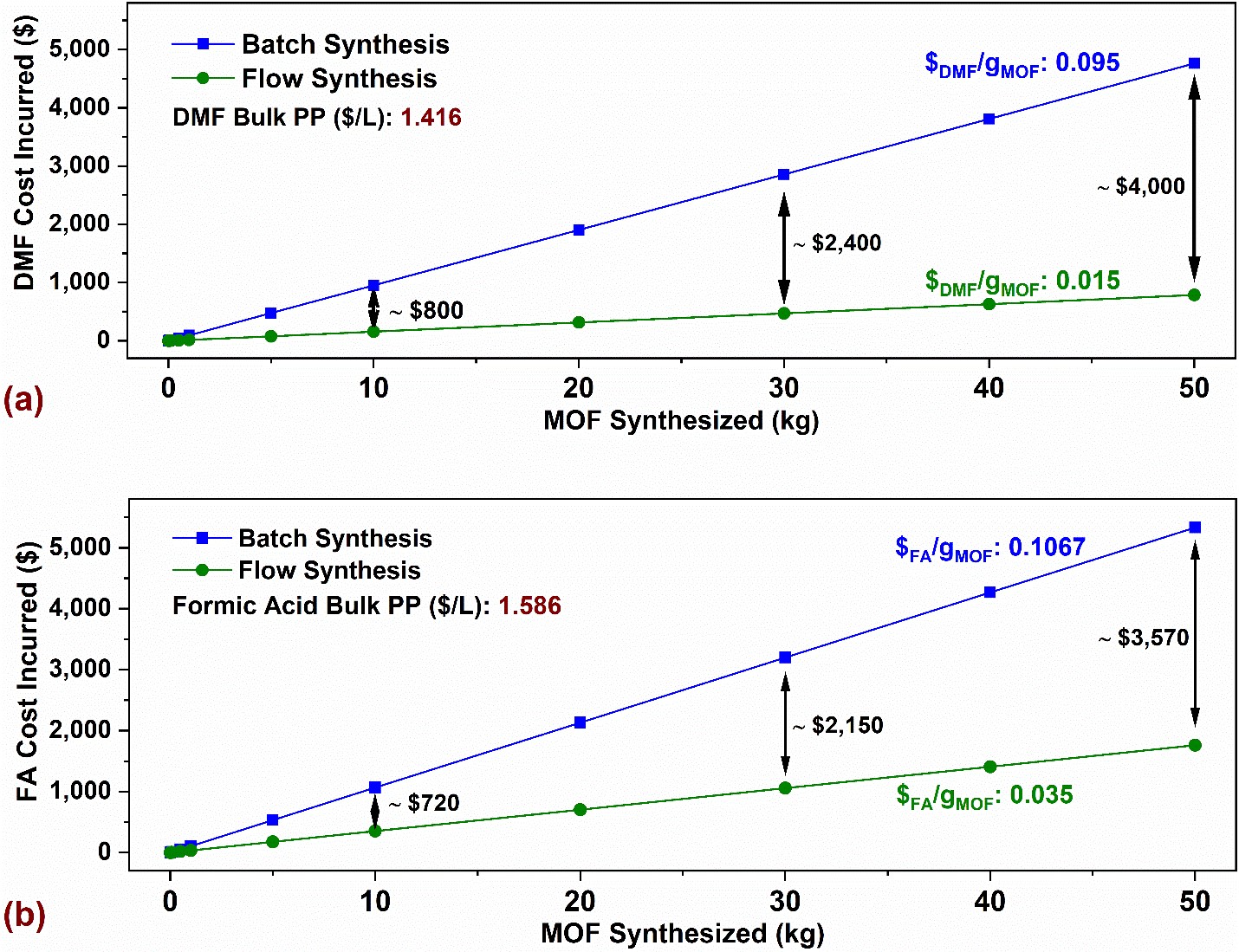
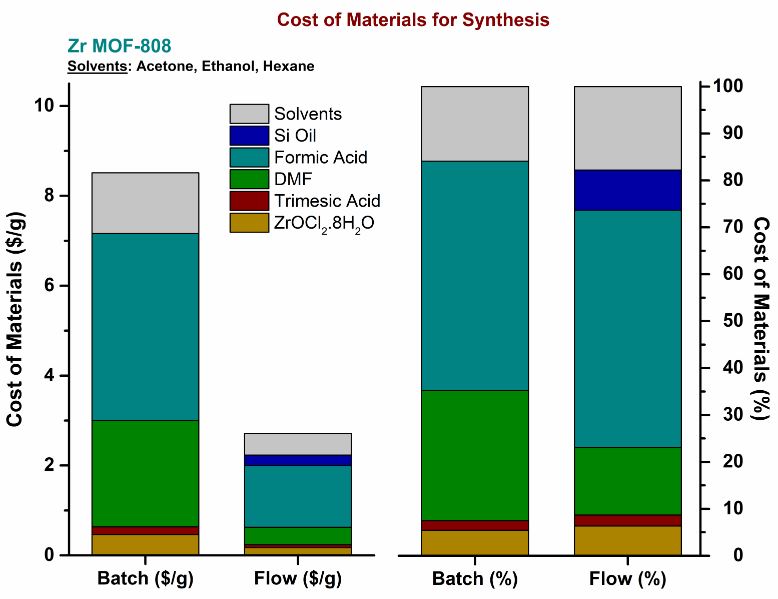
Total cost of MOF synthesis for batch and flow under two scenarios modeled
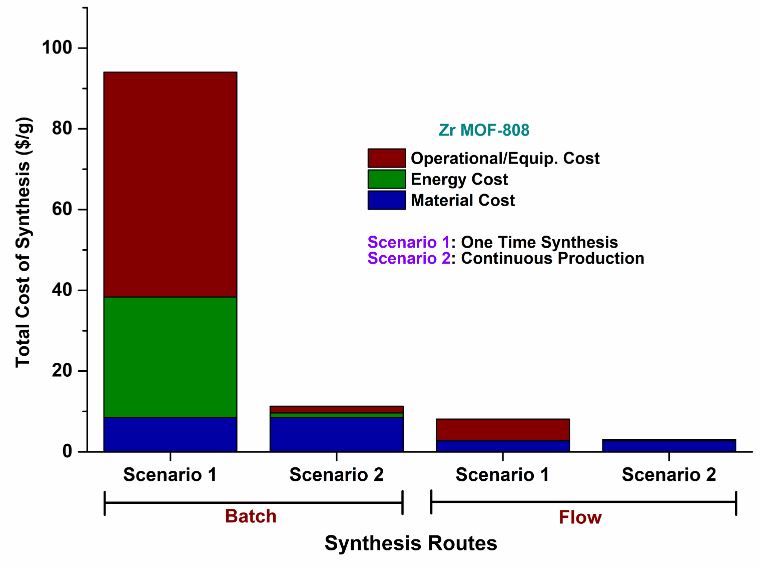