View My LinkedIn Profile
View My Google Scholar
View My Research Lab
I'm a Materials Scientist and a Mechanical Engineer at MIT. My background at the intersection of materials science, mechanical/chemical engineering positions me to understand and efficiently tackle real-world challenges in areas such as crystallization science, materials synthesis, carbon capture, energy storage, techno-economic modelling, automotive emissions, and renewable energy technologies.
View My GitHub Profile
Computing Crystallization Kinetic Parameters
Porous crystalline materials can be broadly divided into three general classes: Zeolites, MOFs (Metal-Organic Frameworks) and COFs (Covalent-Organic Frameworks). Zeolites are microporous aluminosilicates that can be synthesized in a laboratory under hydrothermal conditions as well as found in nature as silicate minerals. MOFs and COFs on the other hand can be synthesized only under solvothermal conditions in a laboratory setting.
MOFs are crystalline coordination complexes consisting of organic linkers and inorganic polynuclear clusters forming highly ordered 2D and 3D structures. Although a large number of MOFs have been synthesized, understanding the self-assembly processes of building units during crystallization has rarely been investigated.
- Performing in-situ or ex-situ studies to probe the rates of crystallization reactions gives us an insight into the rate constants for nucleation and crystal growth. Rate constants can be used to calculate activation energies, which provides information on rate-limiting mechanisms.
- A better understanding of the role played by reaction mixture composition and synthetic conditions can help design efficient crystallization processes to yield desired outcome, vis-a-vis crystal size distribution, production rate, solvent composition etc.
- The reaction mixture for Zr-MOFs such as MOF-808 comprise of a growth modulator (typically a monocarboxylic acid) which regulates the crystal growth, thereby providing additional control on the crystal sizes. However the amount of modulator has to be carefully optimized based on the reactor design (flow vs. batch).
Major Outcomes from the Research
- Employed rapid sampling module developed in-house to quench crystallization reactions performed in flow reactor for MOF-808 (Zr) - an industrially attractive MOF with open metal sites, used in catalysis, heat pumps, separation etc.
- Determined activation energies and rate constants for nucleation and crystal growth using Gualtieri model for solution-mediated transformation.
- Explored the effects of coordination modulation, reaction temperature, & linker concentration on particle sizes.
Relevant Publications for Further Reading
Conversion of XRD Patterns into Crystallization Curves
- Powder XRD pattern for MOF-808 showing miller indices for prominent peaks below 12 degree 2 theta. Area under the curve for peaks corresponding to the plane (400) or (331) is monitored as a function of time to generate crystallization curves for specific reaction conditions. Monitoring the growth of (400) or (331) peaks is well-suited to obtain crystallization curves as they do not overlap with neighboring peaks, and lack features such as pre- or post-edge peaks that may skew the baseline correction and the corresponding area under the curve.
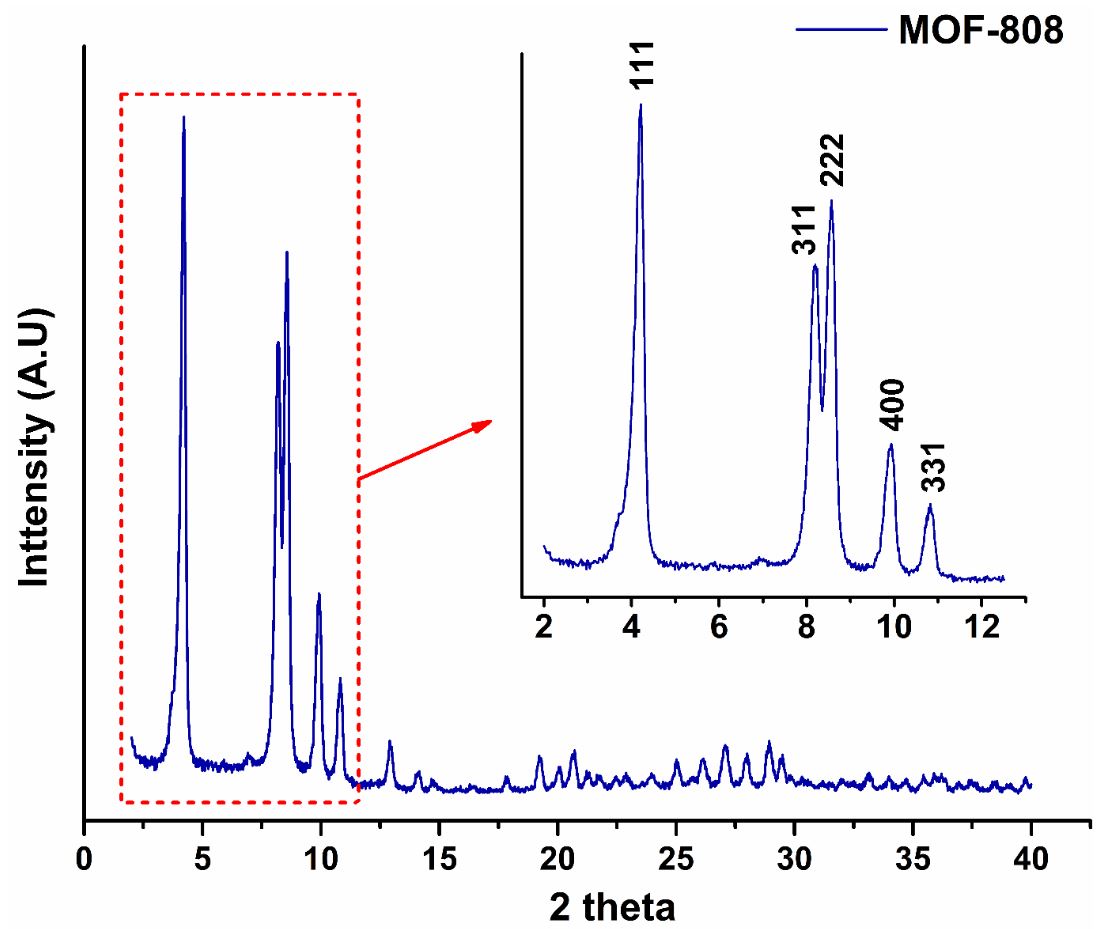
Nonlinear Curve Fitting of Kinetic Data
- Gualtieri model (solution mediated transformation) along with Avrami-Erofeev model (solid-state transformation) were employed to fit the crystallization curves obtained from XRD patterns.
- Fitted models provide values for rate constants of growth and nucleation, which can then be used to calculate activation energies (kJ/mol) using arrhenius plots. Higher values of activation energy translate to a rate-limiting step.
- Extent of crystallization α plotted against time t (closed symbol) and the corresponding Gualtieri fitting (red curve).

TEM Image used for Estimating Crystal Size Distribution (CSD)
- TEM images were acquired for every synthetic condition from different regions on the copper grid (sample holder). An average of 500 particles were measured for all reaction conditions to generate a CSD and a standard distribution.
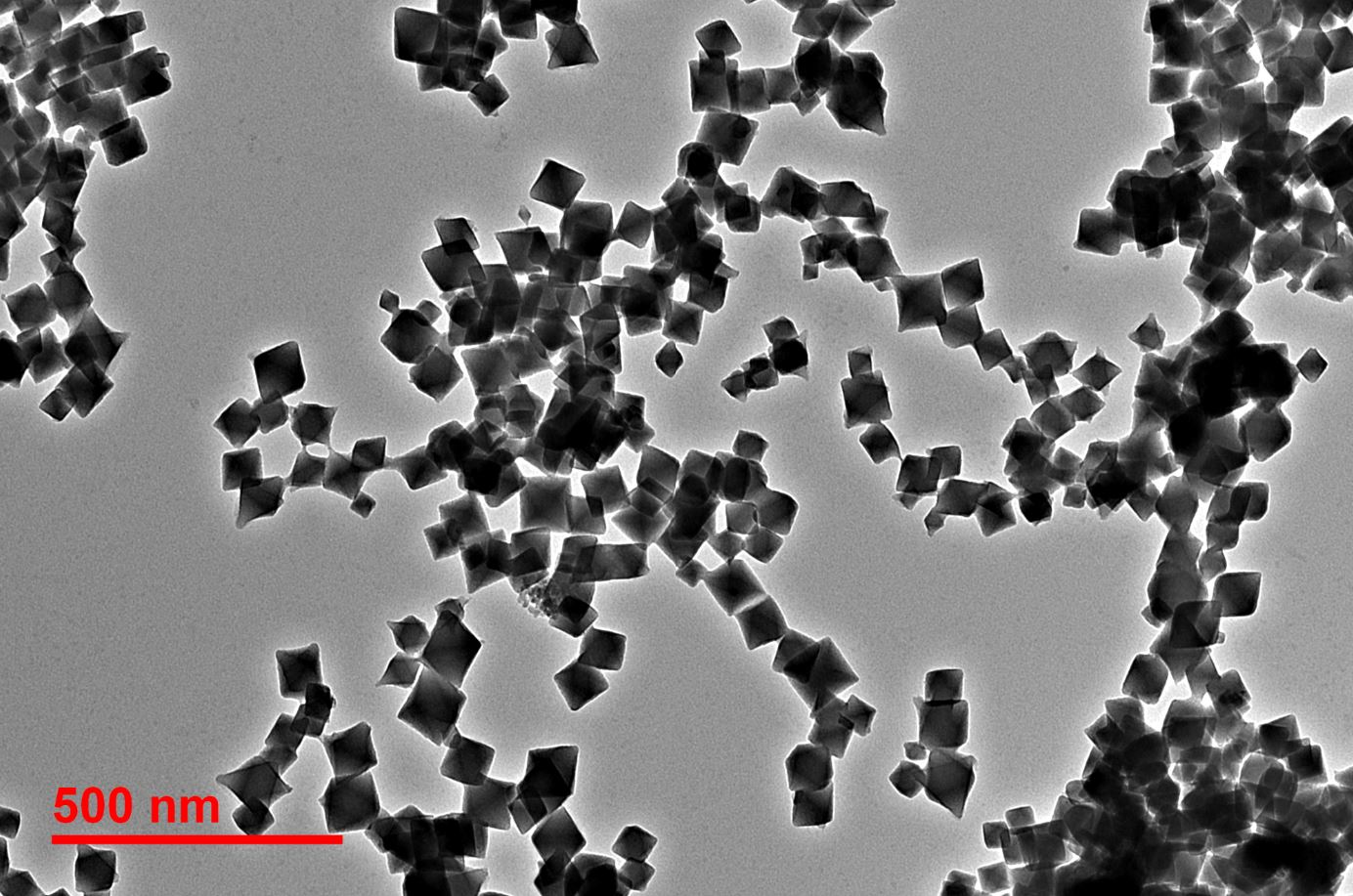