View My LinkedIn Profile
View My Google Scholar
View My Research Lab
I'm a Materials Scientist and a Mechanical Engineer at MIT. My background at the intersection of materials science, mechanical/chemical engineering positions me to understand and efficiently tackle real-world challenges in areas such as crystallization science, materials synthesis, carbon capture, energy storage, techno-economic modelling, automotive emissions, and renewable energy technologies.
View My GitHub Profile
Investigation of soot-induced wear mechanisms and its effects on diesel engine durability and vehicle fuel economy
- Emissions from heavy-duty diesel engine are classified into four categories: NOx (Nitrogen Oxides–Mixture of NO, NO2, and N2O), PM (Particulate Matter–Carbonaceous soot, ash and volatile organic fraction), CO (Carbon Monoxide), and unburnt HC (Hydrocarbons from fuel and engine oil).
- Most diesel exhaust PM has a primary particle size of less than 50 nm while the agglomerates that are typically more than 100 nm in size amount to less than 5% of the total exhaust particles when weighed by number distribution.
- Part of this soot generated during in-cylinder combustion process bypasses piston rings and leaks into the oil sump of the engine due to blow-by mechanisms in play, while the rest of the soot is trapped by the DPF (Diesel Particulate Filter) placed in the exhaust stream.
- Once soot is in the crankcase, it may interact with reactive degradation compounds or polar additive species originating from the engine oil additives, which in turn may be adsorbed or embedded in the turbostratic soot nanostructure.
- Carbonaceous soot accumulated in crankcase oil is known to have an adverse effect on diesel engine performance, durability, and fuel efficiency. Our studies indicate presence of a three body wear mechanism where engine oil soot trapped between two opposing surfaces in the engine experience extremely high local temperatures and pressure conditions that can induce modifications in crystalline and/or amorphous domains of carbonaceous soot.
- We proposed three predominant wear mechanisms: i) abrasive wear of tribofilms by soot, ii) reduced lubricity of engineoil due to adsorption of metallic species on soot surface, and iii) competition of soot with polar additive species to adsorb on interacting metal surfaces thereby hindering formation of tribofilms.
My contributions to the field
- My recent recearch publications (web-links below), focus on probing the role of engine oil additive package on minimizing soot-induced wear. We perform engine-dyno tests to investigate the interactions between crankcase soot with polar species in lubricant additive formulations. We correlate the surface chemistry of crankcase soot, structure, morphology, and oxidative behavior with vehicle operation. This helps us in developing better oil formulations that are tailor-made for specific engine/duty-cycles offering enhanced wear protection and improved fuel economy (by reduced oil thickening).
- Our studies serve as a benchmark in the field of materials characterization for crankcase and exhaust soot, where methodologies presented can be utilized as a template for others to follow and build off of the results.
- With my previous experience working at a heavy-duty diesel engine OEM, I recognize a wide gap existing between the results obtained from controlled laboratory-bench tests and real-world testing when it comes to formulating an appropriate additive package for robust engine performance. Our research has helped in minimizing these knowledge gaps taking us a step closer to elucidate the complex interactions between lubricant oil and PM in diesel engines.
Relevant Publications for Further Reading:
Temperature-resolved X-ray diffraction to characterize soot oxidation
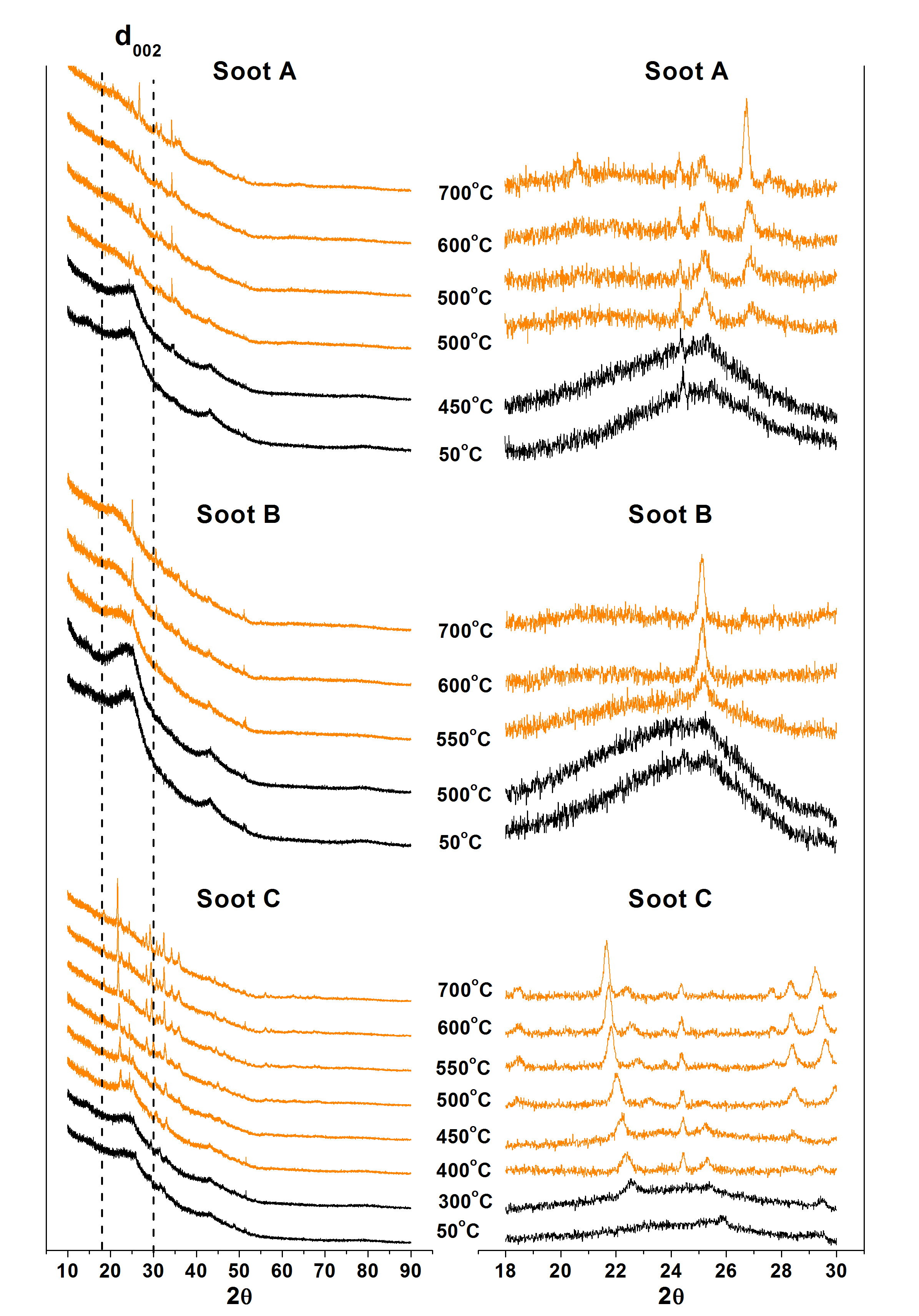
Tracking the variation in inter-planar lattice spacing of 002 plane
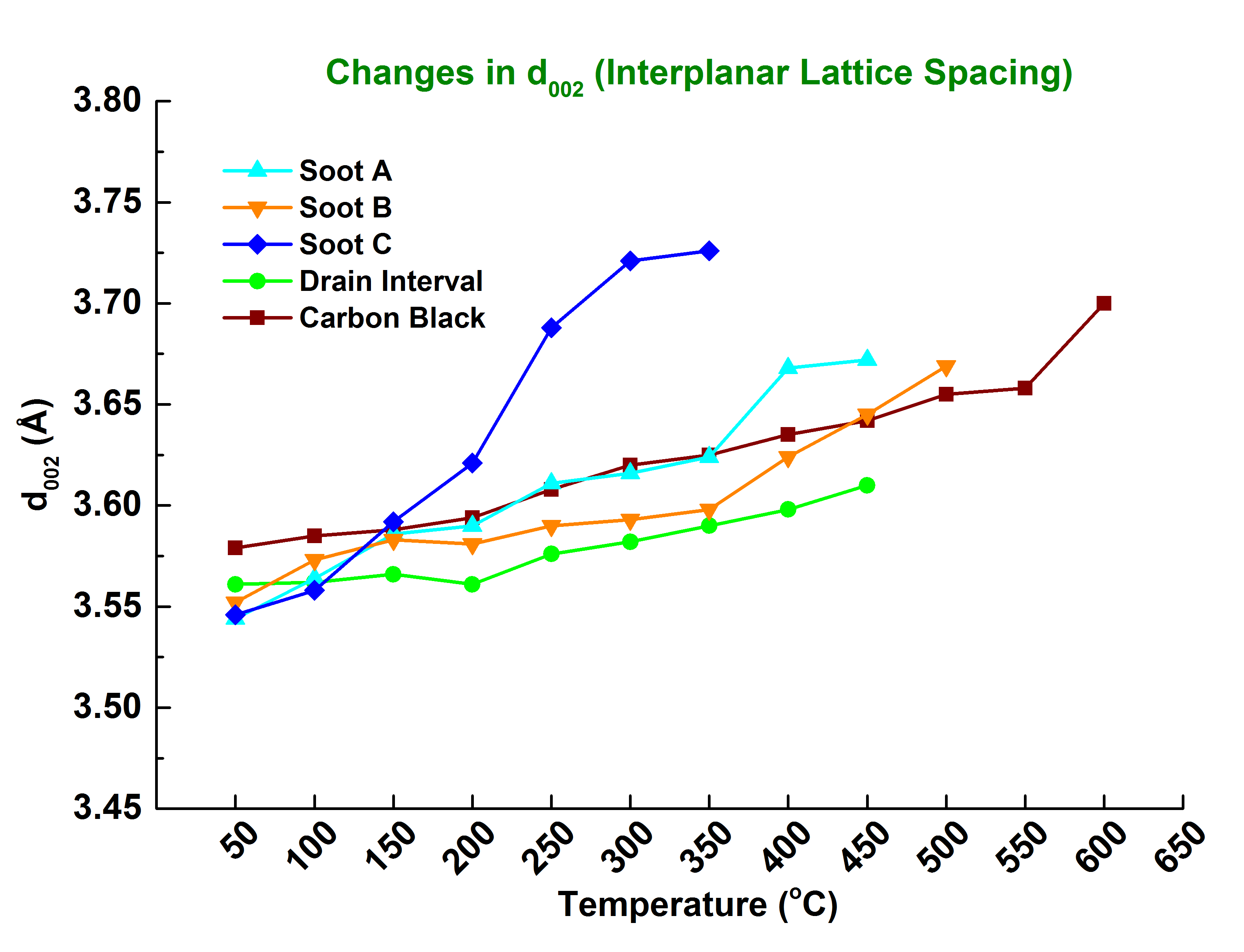
Heavy-duty Diesel Powertrain in an On-road Class 8 Truck
