View My LinkedIn Profile
View My Google Scholar
View My Research Lab
I'm a Materials Scientist and a Mechanical Engineer at MIT. My background at the intersection of materials science, mechanical/chemical engineering positions me to understand and efficiently tackle real-world challenges in areas such as crystallization science, materials synthesis, carbon capture, energy storage, techno-economic modelling, automotive emissions, and renewable energy technologies.
View My GitHub Profile
Fast Optimization of Synthesis Space
- Synthesis space or reaction space refers to a critical range of process parameters such as molar ratios of reagents in the precursor mixture, residence time, and reaction temperature that dictates the outcomes such as product crystallinity, production rates, crystal size distribution etc.
- In most cases involving synthesis of Zeolites or MOFs, there are a large number of parameters to screen; parameters with small response factors are usually held constant while rest of the parameters can have a specified range where experiments are run.
- Below is a test case for Ni2Cl2(BTDD) MOF, wherein we use DoE (Design of Experiments) to build an experimental matrix of 45 tests to screen 4 critical process parameters are screened using a continuous flow chemistry platform.
- Highly crystalline regions on the synthesis maps that result in lower use of expensive solvents and short residence times, translate to energy-efficient and low-cost manufacturing routes thereby optimizing the existing process to a ‘greener’ alternative.
Major Outcomes from the Research
- We developed a modular fast-sampler unit connected to the outlet of the flow reactor, which increased the sampling frequency. This feature enables obtaining time-resolved studies of crystallization processes by screening the effect of multiple synthesis parameters in a short duration.
- We reduced the amount of solvents in the reaction mixture compared to the optimized batch composition, thereby leading to significant cost savings and a greener process. The flow process reduced the volume of Methanol and HCl used by 50% and 40% respectively to synthesize the same amount of MOF.
- Flow process resulted in a yield of 80%, compared to 75% yield obtained in Batch. The process productivity is defined in kg/m3/day (kg of MOF synthesized per m3 of reaction mixture per day). Flow process productivity was 0.765 kg/m3/day compared to 0.245 kg/m3/day obtained in Batch.
Map of synthesis space investigated for Ni2Cl2(BTDD) using flow synthesis varying (a) reaction temperature and residence time; and (b) volumetric ratios of Methanol:DMF and HCl:DMF obtained at 140 °C and 60 min residence time
- Labels for every data point represent the relative crystallinity in percentage (% RC), that quantifies the amount of crystalline phase in the synthesized product.
- Parameters such as the residence time and reaction temperature were varied in a range of 15 min to 240 min, and 120-150 °C respectively, based on synthesis parameters reported in previous literature.
- The synthetic condition in flow with the highest yield of crystalline Ni2Cl2(BTDD) is labelled 100% RC, while RC values calculated for rest of the synthetic conditions were divided into three categories: >80% RC were classified as crystalline, 30% < RC < 80% classified as semi-crystalline, and RC < 30% were classified amorphous.
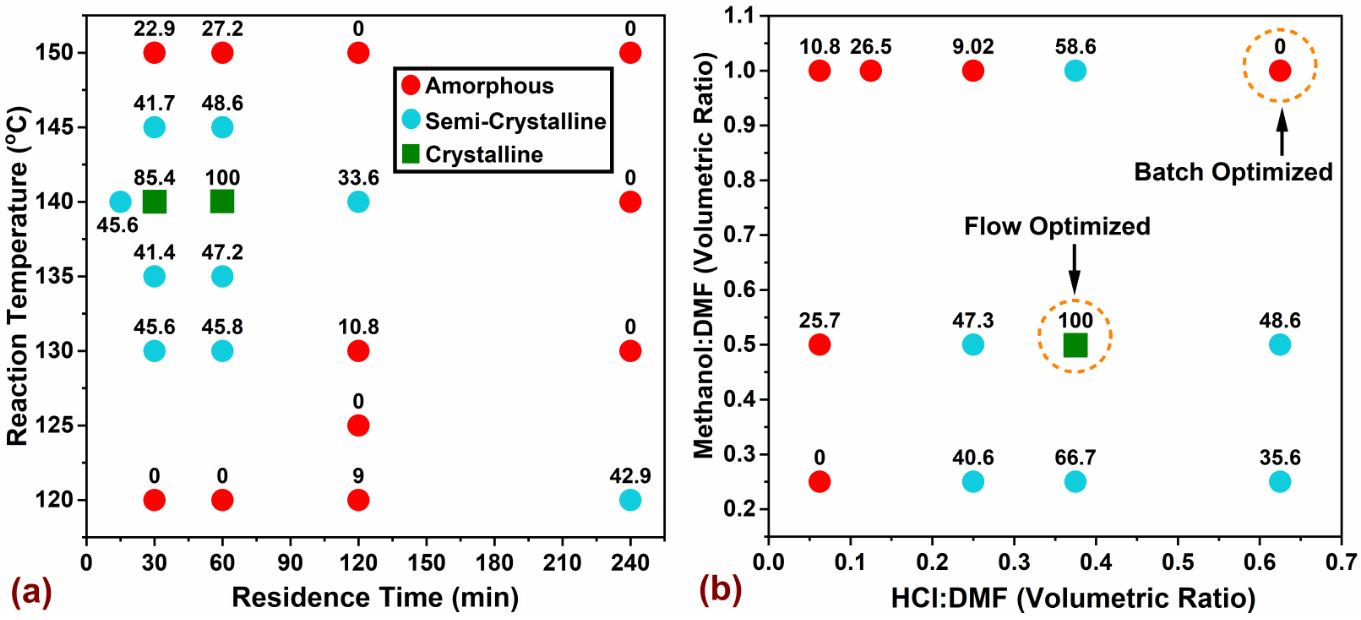
Background correction scheme used to quantify intensity contributions from crystalline domains in the XRD pattern obtained from the sample
- Relative crystallinity in percentage (% RC), quantifies the amount of crystalline phase in the synthesized product. The RC is determined from a ratio of intensity contributions originating from the crystalline phase calculated using an iterative background correction method to the total intensity from the PXRD patterns.
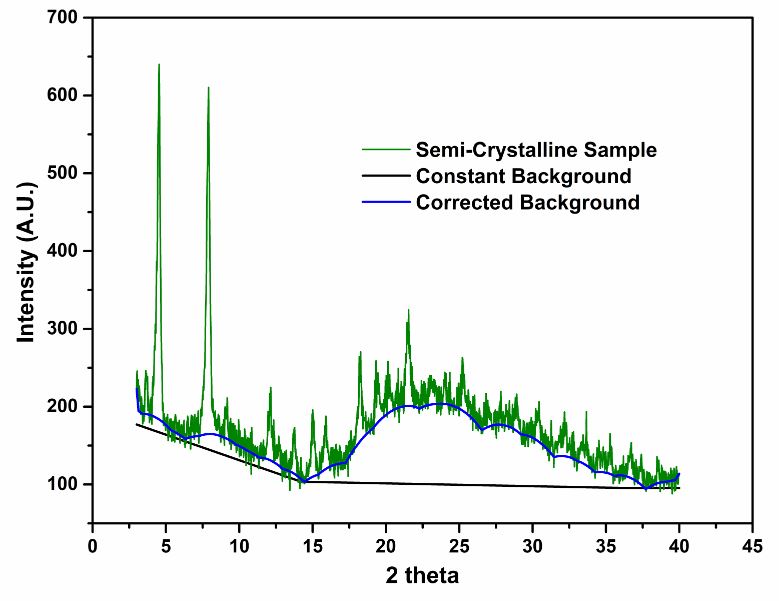
TEM images of Ni2Cl2(BTDD) synthesized in batch (a-c) and flow (d-f), confirming the needle-shaped morphology of the crystals
- TEM images for the optimized conditions in both batch and flow routes are compared to ensure the samples maintain their structure and morphology.
- The TEM was operated at 120 kV and corrected for image aberrations using stigmator in condenser/objective lens.MOF sample dissolved in acetone was placed on a Cu-grid and dried before imaging.
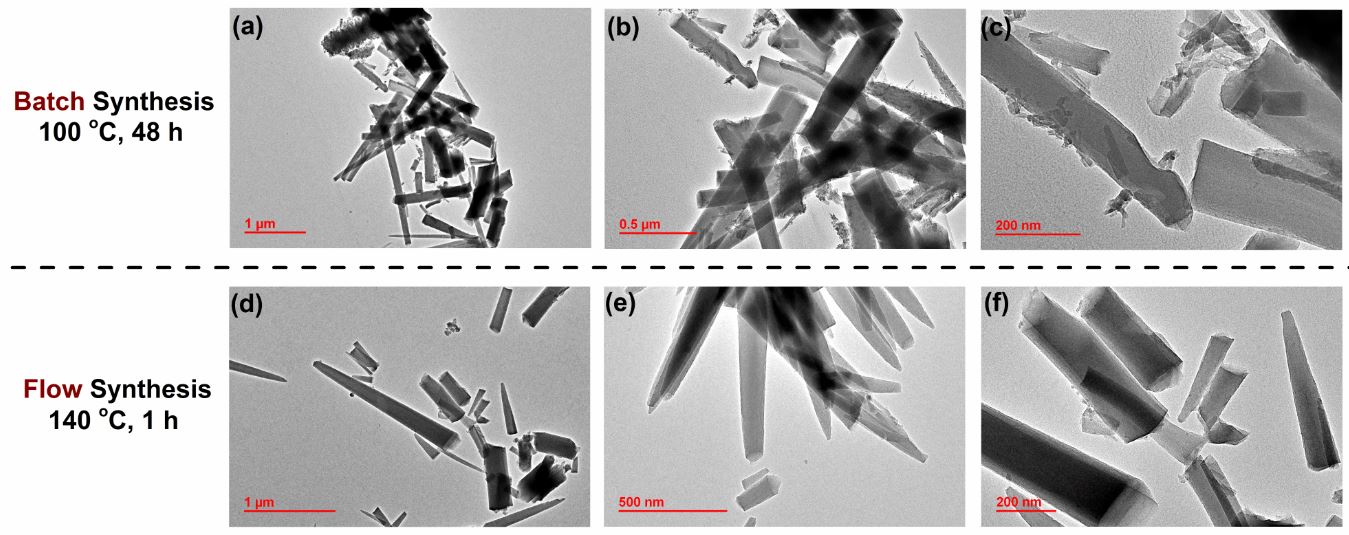